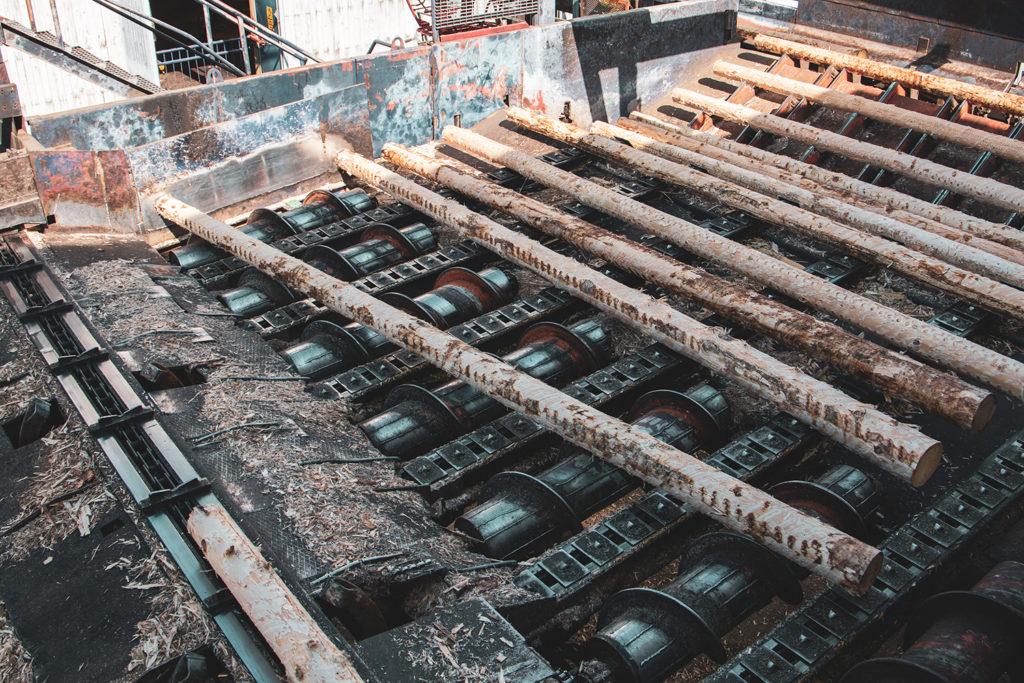
A new debarking machine has been purchased for the Järvelä mill and tuned to perfection during the spring and early summer. The machine is manufactured by Valon Kone, and it is a rotor debarker, which is the most common and cost-effective debarking method available. Rotor debarking is also the gentlest method available, and is therefore well suited for the needs of the sawmilling and plywood industry.
“It was a pure replacement investment,” says Timber Industry’s Production Director Lassi Santala. “The old machine was run-down, and the repair costs would have been intolerable.” The old debarking machine was commissioned in 1995, the year of Finland’s first World Championship in ice hockey, and it had processed more than 10 million cubic metres of spruce and pine logs. The capacity of the new machine is equal to the old one. “There is no sense in choosing a machine with excessive capacity in relation to production,” Santala points out.
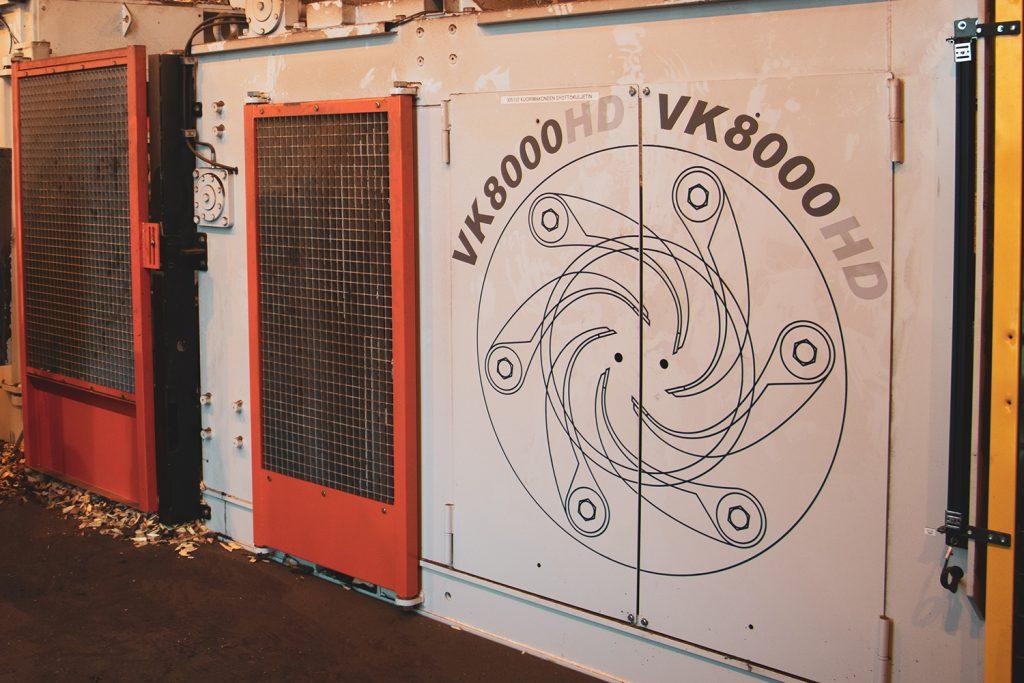
The basic task of the new machine remains the same. “The operating principle is largely identical, and the process itself has not changed.” Nevertheless, the machines have come a long way in 20 some years. As a result, the new debarking machine’s level of automation is higher. “In the old machine, the debarking pressure was generated hydraulically, but the new one is pneumatic. In the new machine, the tools can be opened, and the log can be stopped inside the machine, if necessary. With the old debarking machine, more raw material was wasted because the hydraulic control of the debarking pressure was less precise,” Santala explains.
Debarking result is the key
Debarking improves the processes of modern production plants in several ways. A common reason for debarking is related to quality requirements concerning the woodchips produced as a by-product. Thus, the debarking result is the key. “The new machine ensure gentler debarking, and there is less damage to the logs. This translates directly into higher quality sideboards,” Koskisen’s Product Director Jaakko Huttunen points out. As far as production is concerned, the new debarking machine has improved raw material yield, and the amount of valuable wood among bark, which is incinerated, has decreased.
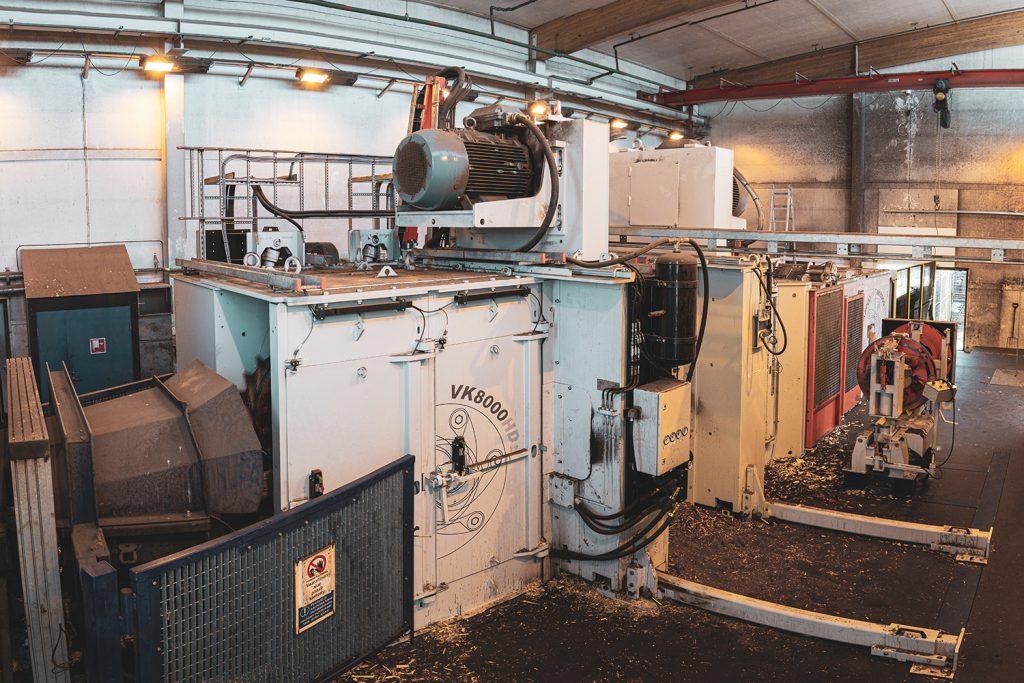
“We were looking for debarking results that are sufficiently good, not overly good. The new machine is also an improvement in terms of adjustability,” Santala says. “The ability to adjust the debarking pressure helps us prevent wood raw material waste. However, insufficient debarking results in too much bark among the chips destined to pulping processes. We are continuously optimising the process.” The chips, which are used as raw material by the pulp industry, must be sufficiently clean to be suitable for producing pulp, which is then further processed into paper.
Replacing the old debarking machine caused a nine-day production stop in the debarking line, as the old machine was dismantled, the foundations altered and the new machine installed, electrified and tested. The crew had to work around the clock under a tight schedule. The installation was followed by test runs. “We worked hard to find the correct tip angles. The seventh set of tips turned out to work well,” Santala says. Koskisen is now happy with the new machine in all respects. Valon Kone gets their share of the praise. “They have active product development, and their project execution is first class,” Santala says.