Koskisen’s Finnish chipboard products have the most comprehensive selection of chipboards for construction, interior design, and the furniture industry. The sawdust used as raw material at Koskisen’s chipboard factory mainly comes from its production, as sawdust, a by-product of plywood and sawmill production, is delivered to the chipboard factory as raw material. The appreciation of this valuable raw material is also reflected in this: Koskisen doesn’t let even sawdust go to waste, according to the Sawn Timber and Panel Industry.
A Sawmill industry by-product tied to long-cycle carbon products
“Many sawmills sell their sawdust for combustion, or the sawdust goes as raw material for the pulp and paper industry. In our case, most, if not all, is used for our use and tied to long-cycle carbon products,” says Tommi Sneck, Director of Koskisen’s Sawn Timber Industry.
The use of wood in construction, for example, extends the natural cycle of carbon. The carbon stored in the products is out of the cycle for the life of the product and is only released into the atmosphere as carbon dioxide when the product decomposes, for example by burning or rotting. In construction, wood products have a long service life.
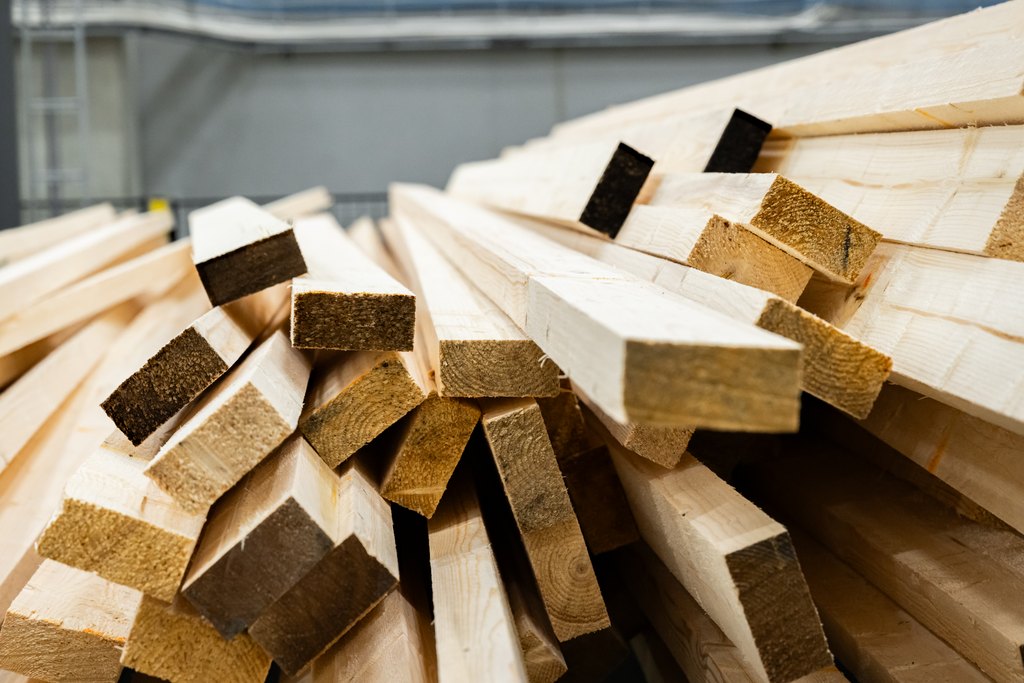
Purely Finnish chipboard
Koskisen has the only chipboard factory in Finland in Järvelä, and most of the production remains in Finland. Our customers therefore also receive purely Finnish and sustainably produced chipboard, reminds Tom-Peter Helenius, Director of Koskisen’s Panel Industry.
Helenius also lists the transparency and traceability of the end-product as benefits of Koskisen’s chipboard products. Koskisen’s chipboard products have also been awarded the Nordic Swan Eco Label.
The by-product of Koskisen’s industry is also of very high quality when viewed more broadly. While in Central Europe, chipboards can contain a lot of impurities from recycled wood, Koskinen’s product does not have this.
“Our chipboard is literally one of the cleanest. Thanks to this, it is easy to process and more cost-effective for our customer in the long run, as the customer’s machine tools and their blades stay in better condition for longer,” says Helenius.
