This past summer, Koskisen focussed strongly on a new X-ray log scanner at its log sorting facility. Preparations for the new X-ray log scanner were initiated already the previous spring, and included the full-time recruitment of Kirsi-Marja Toivonen, who is writing her Master’s thesis on the subject. Kirsi-Marja’s assistance helped to ensure that the investment would bring the greatest possible benefit right from the start. The X-ray log scanner was finally in full use on the sawmill’s sorting line at the end of August.
“The technology has evolved tremendously in recent years, and the machines have become more and more compact. For those reasons, it was the right time to invest in one,” says the sawmill’s Production Manager, Jaakko Huttunen.
Compared to the previous sorting method, the X-ray log scanner clearly enhances efficiency in both log sorting and the utilisation of the raw material. The X-ray log scanner enables more efficient sorting and sawing of the pine and spruce logs that arrive at the sawmill, which means there is also less log waste.
“In sawing, the raw material costs represent a significant share of the price of the final product. The goal is therefore to get the most out of the log materials,” says the sawmill’s production planner, Juha Virmiala.
In addition to costs, sustainability issues were also considered. With wood consumption continuously increasing in Finland, it is important to make efficient use of all the raw material obtained from forests, and to process higher-quality products from the best-quality logs.
Better opportunity to produce customised grades
The X-ray log scanner measures bark thickness and reveals the inner quality of the logs, the location of knots, the heartwood diameter and clear differences in density. Since the X-ray log scanner is able to calculate the top diameter of the log under the bark, it possible to more accurately determine how to efficiently saw the log.
“The X-ray log scanner allows us to sort the logs so that we achieve the optimal sawing grade in terms of the final product and the customer’s specifications. At the same time, it gives us the opportunity to produce customer-specific grades,” explains Huttunen.
Koskisen has devoted considerable resources to the X-ray log scanner project. Kirsi-Marja has been involved in the project almost full-time since the spring. Virmiala and the sawmill’s foreman, Anna Vilkko, have also been assigned to the project. Another partner in the project is RemaSawco Oy, the company that delivered and installed the X-ray log scanner on the Järvelä mill’s log sorting line.
“We knew this would be a challenging project, so we wanted to dedicate our best experts to it. It really paid off, as in the very first pine sawing we were able to see how the X-ray grading works. The timber sawn from A-graded butts was U/S quality to a very high degree,” says a pleased Huttunen.
For now, harvesters measure the logs as they are harvested. X-ray log scanning, however, offers opportunities to grade and price the logs.
“In principle, it will be possible in the future to use X-ray log scanning to determine log quality and log pricing when receiving the raw material, in which case the value of the raw material would be defined even more precisely,” reckons Huttunen.
Captions:
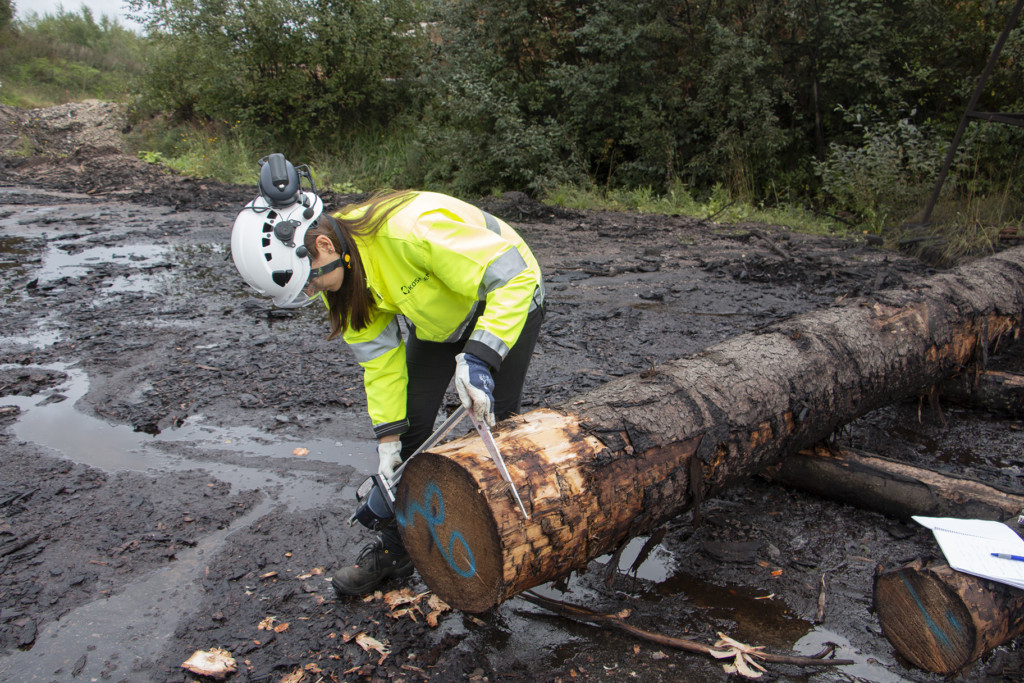
Koskisen employee and Master’s thesis worker Kirsi-Marja Toivonen makes measurements on logs sorted by the log X-ray machine.
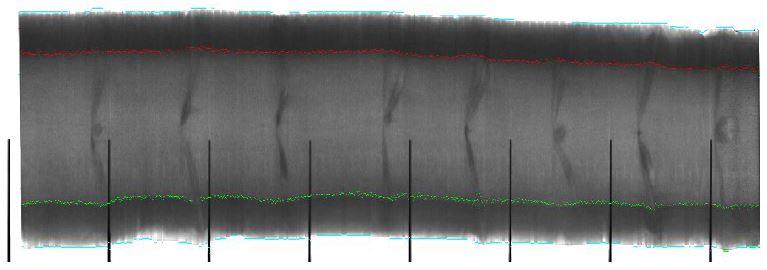
An image of the inside of the log produced by the X-ray log scanner. Image: RemaSawco Oy
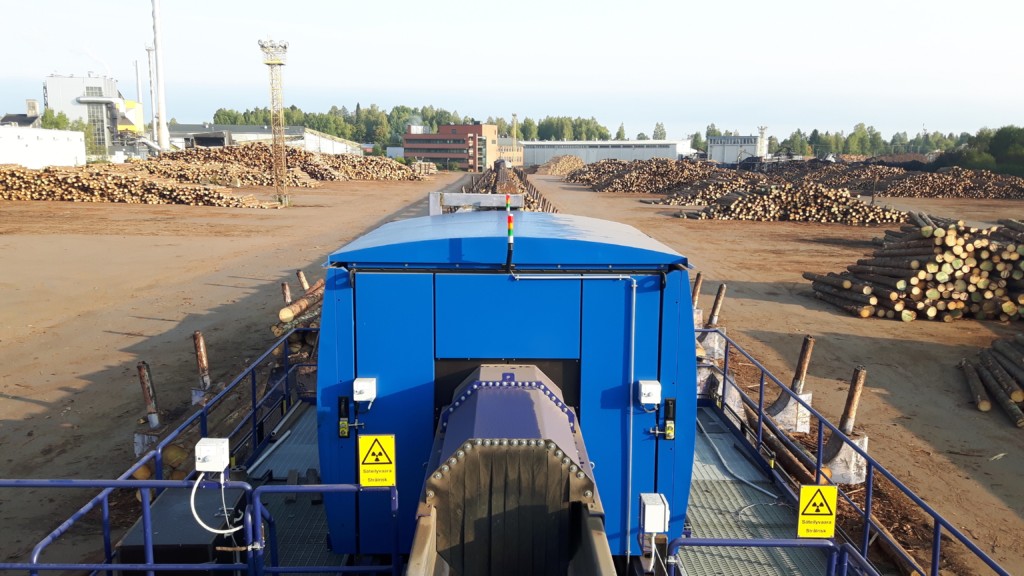
Every day, thousands of cubic metres of logs pass through the log sorting line at Koskisen’s Järvelä mill.